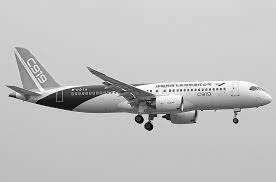
Raghu
IT has been some time coming, but China’s first large home-made passenger jet finally entered commercial service last week on May 28, 2023 on a China Eastern Airlines flight from Shanghai to Beijing. The C919 jetliner, with a 156-168 seat capacity and a nominal range of 4000-5500km, is made by State-owned Commercial Aircraft Corporation of China or COMAC. It is a single-aisle narrow-body passenger aircraft positioned to compete with the Boeing 737 and the Airbus A320.
By western aviation industry standards, China has taken a long time, 15 years, from 2008 when the project and COMAC itself were launched, to 2017 when the aircraft flew for the first time. However, for a country and a company which are making such an aircraft for the first time, with numerous issues being encountered and having to be dealt with for the first time, this timeline should be considered reasonable. Whereas full details are not known, and indeed cannot be known in as sensitive an industry as aviation, that too in China, the trajectory of design-development of the C919 is highly instructive about how China approaches technology development in a strategic and high-tech area. In particular, there are also many lessons for India which, at least on paper, also has a similar goal of technological self-reliance.
HOMEGROWN AND FOREIGN TECHNOLOGIES
The C919 is a major step forward in China’s determination to develop advanced technologies matching those in the West. China had already developed several military aircraft and a few smaller civilian jets, notably the Comac ARJ21, a short-haul or regional 78-90 seat aircraft mostly for the domestic market. The C919, however, is a larger medium-haul passenger carrier aimed at taking on and competing with the global duopoly of Airbus and Boeing in that market segment and is therefore a different kettle of fish.
We should first note that the airframe, wings and tail are entirely indigenous. Many aviation analysts point to the overall silhouette appearance being very similar to the Boeing 737, and to external dimensions being similar to the Airbus A320, to the extent that the A320 and the C919 may be able to use the same unit loader system used to load the aircraft with cargo, baggage, supplies and so on. It is believed that Comac used the Tianhe-2 supercomputer for designing the airframe and its aerodynamics, including what is called a supercritical wing which significantly improves the aerodynamic efficiency and reduces drag caused by the build-up of a supersonic shock-wave along the wave even though the aircraft itself is flying at subsonic speeds.
On the other hand, we should also note that, although hailed as a path breaking indigenous achievement, about 60 per cent of the C919’s components, including its most important elements, are of foreign, mostly US, origin. Most importantly, the C919 uses the CFM LEAP 1C engine made by the 50-50 collaboration between France’s SAFRAN and General Electric of the US, currently the world’s largest selling aero-engine used in several variants of Boeing and Airbus aircraft including the Boeing 737 Max and the Airbus A320 neo, the former suffering badly due to its own design problems and also largely due to the PW1000G engine made by GE’s giant US rival Pratt & Whitney.
China is simultaneously developing its own ACAE CJ-1000J starting from 2009. Most observers believe, however, that China may still be at least 10 years away from completing development of this engine proving what is well-known in aviation, namely that turbo-jet aero-engines are the most complex technology of an aircraft and the most difficult to develop. Only the US, UK, France and the Soviet Union/Russia have this capability for larger civilian and military aircraft. Even China’s smaller ARJ21 is powered by General Electric’s GE CF24 engines. China’s military aircraft the J7or MiG-21 under license, the JF-17 using a Klimov RD93 and its “fifth generation” J20 fighters are powered by Russian Lyulka-Saturn AL-31 engines or domestically adapted variants.
Several poorly-informed critics have belittled India’s Tejas Light Combat Aircraft (LCA) for having about the same percentage of foreign technologies or systems. The real question to ask, however, is whether and how the extent of indigenisation is proposed to be increased. On this count, China’s plan for C919 appears to be more future-ready, partly due to the larger scales available to a civilian aircraft compared to the more limited production of a fighter aircraft in India, and partly to the domestic technology and manufacturing base available or being prepared in the two countries.
PHASE-WISE INDIGENISATION
Of the other major components or sub-systems, the engine nacelle or shell, advanced inlet systems, thrust reverser and exhaust system are by France’s Nexcell, the integrated modular avionics, air-conditioning and landing gear are by Germany’s Liebherr along with its Chinese collaborator. Many other components or sub-systems are made by China-based joint ventures with foreign companies such as with US firm UTAS for electrics, Rockwell Collins for cabin systems and avionics, Honeywell for fly-by-wire systems, flight controls, auxiliary power systems and brakes, and with Parker for hydraulics, actuators and fuel systems. Canadian aviation major Bombardier has provided overall consultancy on supply chains, electrical systems, cockpit, flight training, human interface, sales and marketing. Along with the engine, China is determined to and is moving to ultimately indigenise all these sub-systems too.
Without getting too technical, what this shows is that China has, over the years, built up an extensive aviation industry and component or sub-systems eco-system comprising Chinese companies in collaboration with US, French, British and other specialised foreign majors. China also has an Airbus A320 assembly line and makes several elements of Boeing airliners. China has managed to acquire these assets by leveraging its massive orders for Boeing and Airbus, nowadays mostly the latter, and compelling these aviation majors to set up assembly lines, sub-assembly and component manufacturing joint ventures. It appears that elements of such a supply chain have been strategically identified and positioned in the domestic manufacturing ecosystem so that, one day, they come together and enable an indigenous structure.
It should also be noted that China has, in a planned manner, reverse engineered these and other technologies so as to indigenise the know-how. This is easier said than done, and involves much more than just copying a design. Despite years of license manufacturing of foreign military hardware in India, this kind of reverse engineering and technology absorption has not been achieved. Nor has India’s large domestic market, next only to China’s, been adequately leveraged to obtain concessions, domestic manufacture and technology transfer.
Whether true or not, US companies and the government have also long accused China of industrial espionage, and hacking of their collaborators’ systems to get at proprietary technologies, with some Chinese nationals and their agents also having been caught, tried and sentenced for stealing company secrets.
Whatever the truth of these accusations in a diplomatic, commercial and strategic world where mutual espionage, even between allies, is widespread, all these measures taken by China show that it is determinedly pursuing its “Made in China 2025” strategic plan announced in 2015, to become a global player or leader in manufacturing of advanced technologies including aviation and avionics.
China is playing a long game here. To achieve its goal of developing and making an indigenous passenger aircraft, China has first set up a domestic manufacturing base pressurising foreign companies to enter collaborations by leveraging large domestic orders, then using these collaborations to develop indigenous technologies, and finally sometime in the future indigenously developing its own aircraft. With the C919, China appears to be somewhere between phases 2 and 3.
In contrast, at least going by history to date, India appears unable to cross-over from Phase-1 and transition towards Phase-2, the last phase being a far cry away.
LESSONS FOR INDIA
In broad terms, India has shown a lack of determination to pursue the goal of technological self-reliance in aviation, both military and civilian. For many decades since independence, India remained satisfied in serial license-production of foreign military aircraft, especially given limited numbers especially for western fighters. In both western and Soviet/Russian aircraft types, India refrained or allowed itself to be pressured to avoid reverse engineering or any other strategy to acquire technology, especially design capability.
After liberalisation in the 1990s, India decided to open up to FDI in defence manufacturing, including up to 100 per cent, in the belief that this would tempt foreign majors to set up manufacturing bases in India but to no avail, since the foreign majors were looking for larger volumes and could not be otherwise be tempted to transfer technologies. India also badly handled its offsets policy for military orders, in which offsets should have been used strategically for developing a domestic manufacturing ecosystem for components and sub-assemblies. Instead of dictating terms to foreign suppliers leveraging the substantial orders, India allowed itself to be pushed into allowing the suppliers to select their own offsets projects where only commercial rather than strategic interests were involved.
India seriously missed the bus in civilian aircraft in which it had a far more attractive large-volume demand from domestic airlines. Already, domestic carriers have placed huge orders of over 1500-2000 aircraft, with projected demand of more than 6,000 aircraft over the next couple of decades. This provided a massive incentive for indigenous design and development of civilian passenger aircraft, with provision for foreign collaboration, gradual technology absorption, large manufacturing ecosystem and finally completely indigenous aircraft development.
These very columns, more than a decade ago, had urged development of a roughly 90-100 seater passenger aircraft, followed by design-development of a 150-160 seater aircraft, more or less the trajectory followed by China. Shortsightedness of the aircraft industry, aversion to risk on the part of the government, and overall timidity of all stakeholders prevented such a goal-oriented path. This is still possible, but are there any takers?